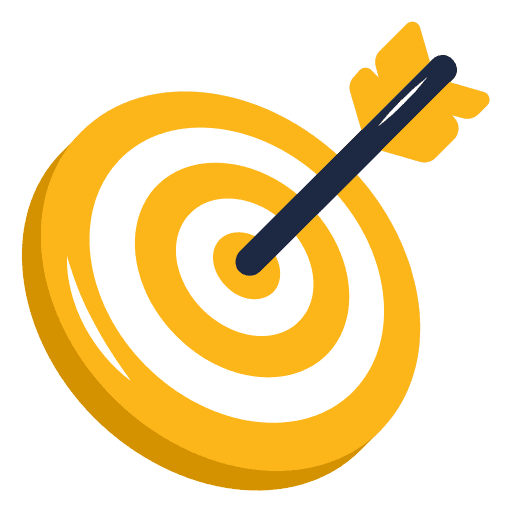
1
Understand ARM’s step by step process when working on a project with a manufacturer
2
Discover factors and pain points that contribute to the slow adoption rate
3
Identify key stakeholders in manufacture and their workflows and pain points
Internal Challenges: Gain insights through client meetings
20+
pain points identified from our clients by doing research activities including Speed Boat and Bulls-Eye Diagraming
External Challenges: Understand through site visits and field studies
30+
interviews with diverse external stakeholders, such as facility managers, engineers, and operators.
Activities with our client
On-site visit
Synthesize findings
Key Stakeholders & Pain Points
ARM's E2E Process
Identified Problem
The unrealistic expectations of robotics held by manufacturing facility managers, combined with operators' negative perceptions and superficial understanding, result in inefficient collaboration with ARM. Due to limited manpower and time, ARM is often burdened by the time-consuming task of educating these stakeholders on robotics basics. This dilemma leaves ARM torn between their desire to help and the constraints of time, ultimately hindering the adoption of robotics technology.
How might we bridge the robotics knowledge gap between manufacturers and ARM to streamline their collaboration?
Through many conferences, ARM-sponsored events, and manufacturing site visits, we were able to test our prototypes and ideas with various stakeholders such as facility managers, salespeople, operators, ARM team members, etc.
Site Visit at Atlas Metals
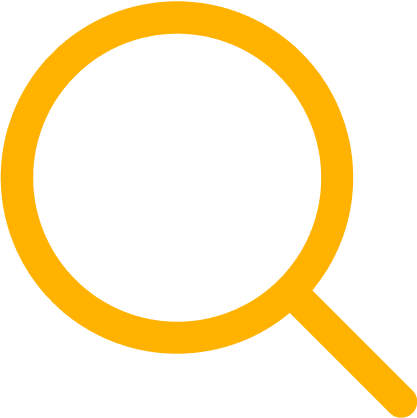
Key Findings
Facility owners greatly appreciate digital, scalable solutions
They like doing activities with their operators and aiding in their education with machinery and engineering
Smart Manufacturing Experience Conference
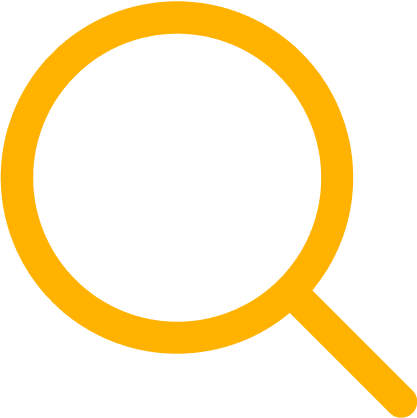
Key Findings
people are generally more interested in ARM’s mission rather than the specifics of robotics information
people generally feel like chatbot should be used for ARM’s mission and to connect with others
Robotics Manufacturing Hub Open House
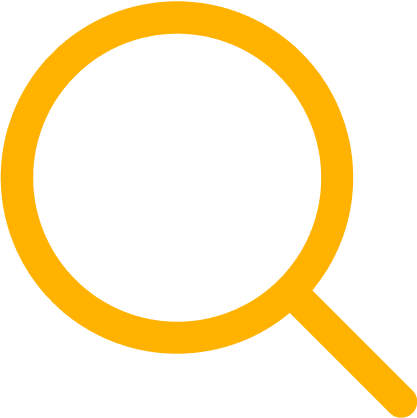
Key Findings
pivoting from the chatbot prototype because of general lack of trust in chatbots
card canvas tool helped co-create value with manufacturers
collaborative learning demo would need to use real imagery/steer away from gamification
Config Conference
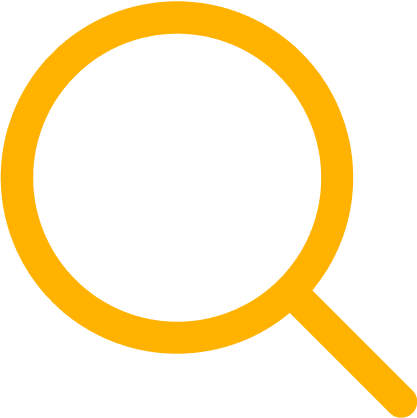
Key Findings
collaborative learning demo tasks to be broken down into smaller bite-sized steps, filmed in-context videos
AR is the way to go because of the motion sickness issues that VR can cause